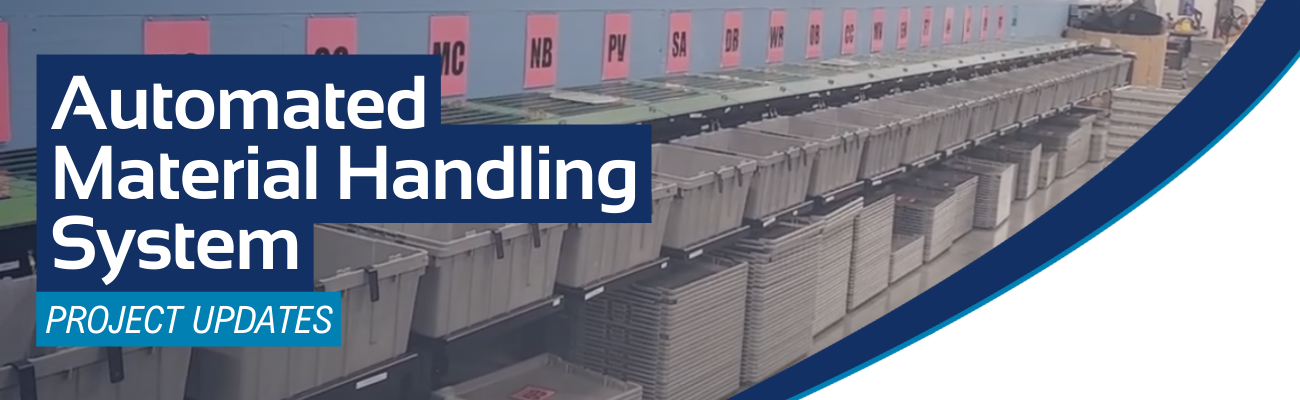
How an Automated Material Handling System (AMH or AMHS) Would Help IHLS Solve Delivery, Staffing, and Budget Problems—
—and how it could help member libraries, too
Since a large majority of IHLS members use a single, connected integrated library system (Polaris, through the SHARE consortium), it makes sense for IHLS to couple the power of SHARE with the power of an automated material handling system. In fact...
93% over 97%
of items sorted by IHLS Delivery come from IHLS-SHARE members!
Using such a system to sort SHARE consortium members' materials could create significant long-term savings to the IHLS budget while improving efficiency overall.
More specifically, IHLS is looking into acquiring an Automated Material Handling System as a potential solution to some delivery, staffing, and funding problems we've encountered. These include:
High turnover rate among sorters • High sorting backlogs after long weekends • Sorting errors resulting in extended delivery times • High rates of worker injury and Workers' Compensation claims • Large increase in volume going through Delivery
The IHLS staff, with the help of a group of IHLS member-volunteers which we refer to as the AMH Working Group, are still estimating costs to make sure that the costs and benefits of purchasing an Automated Material Handling System make sense for IHLS; we're also determining the full costs and benefits of these machines for our members. Our biggest concern is that utilizing an automation system would require portions of SHARE-members' collections (the books and audiovisual items that circulate through IHLS Delivery) to have barcodes somewhere on the outside of those items. Because it wouldn't be fair to place that burden on member libraries (especially when so many of you have only one or two staff members and very small budgets), IHLS is creating a plan for our staff to cover any necessary barcode duplication for you (labor and materials) so you don't have to. If you currently have barcodes on the outside of the items or you have RFID on your items, no barcode duplication will be necessary.
Of course, none of this will happen unless the IHLS staff and board's remaining research leads to the conclusion that the purchase is worth it and IHLS decides to move forward with an installation.
Because it wouldn't be fair to place that burden on member libraries (especially when so many of you have only one or two staff members and very small budgets), IHLS is creating a plan for our staff to do any necessary barcode duplication for you (labor and materials), so you don't have to.
- Learn More About Looking Into an AMH
-
An initial research period of several months resulted in the AMH Working Group recommending proceeding with writing and issuing a Request for Proposal, and the IHLS Board of Directors approved adding a consultant to work on the RFP to the FY2025 Budget. Only after vendor proposals are collected and analyzed will IHLS decide if we should purchase a system.
Using an Automated Material Handling System to sort books would speed up sorting to the point that there would be no expected backlog or delays after holidays and weekends, improve sorting accuracy, and provide ergonomic working conditions for sorting staff, reducing employee injuries due to repetitive movements. It would also require fewer staff to sort items, reducing long-term costs. An Automated Material Handling System looks to be a promising solution.
Depending on the manufacturer/vendor, the size of the system, and any purchased add-ons, the AMH may also have additional capabilities, such as the ability to read RFID codes, sort by returns and holds, and allow for bulk check-in of entire tubs of items.
Because the AMH system integrates with the ILS, and only one ILS, only SHARE-IHLS members' items would be sorted with this system. Standalone IHLS-member libraries' items would continue to be manually sorted. Nonetheless, this would allow the majority of the 3.5 million items sorted by IHLS staff each year to be sorted faster and more accurately by the AMH machine!
Example AMH systems
Some systems by the four companies that responded to the IHLS request for information (individual machine systems vary): Bibliotheca • Lyngsoe Systems • mkSolutions • TechLogic
What do IHLS-member libraries need to do right now?
If you are not part of the SHARE consortium:
- Nothing. Your materials would still be hand-sorted rather than machine-sorted. However, expect to see a long-term improvement in turnaround speed.
If you are a SHARE consortium member:
- Stay informed and stay tuned. Watch the recording of the March 6, 2024, IHLS Members Matter Special Meeting: Delivery Issues and Solutions (including a discussion of the potential Automated Materials Handling System). Read the FAQs below. (Many FAQs were updated on 3/22/2024.)
Special Meeting: Delivery Issues and Solutions
Including discussion of potential AMHS — Recording Now Available
March 6, 2024
IHLS Members Matter Special Meeting: Delivery Issues and Solutions (including a discussion of the potential Automated Materials Handling System)
AMHS Savings/Costs Calculators?
How much will my library save on transit slips?
How much will barcode duplication likely cost my library*?
*if we elect to not have IHLS do it for us
Barcode Duplication Costs Calculator
Share your results with members
Are you willing to share your calculator results with other libraries? Sharing is completely optional. The data shared gives libraries and IHLS some additional insight into the costs of an AMHS system.
Have a question or a concern?
Check out our Frequently Asked Questions below. If you still have a question, contact us at any time!
AMH Project Contact:
Colleen Dettenmeier, IHLS Facilities and Delivery Director (email)
618.656.3216
Frequently Asked Questions
- About Automated Material Handling Systems and Their Benefits
-
- What is an Automated Material Handling System (AMH / AMHS)?
-
In warehouses and distribution centers, the term "Automated Material Handling System" (or "AMH" or "AMHS") generally refers to a tool, or system of tools, that removes the need for manual interaction to check in, check out, move, catalog, or sort materials. This provides greater efficiency and accuracy than manual handling alone can offer. For IHLS, "Automated Material Handling System" refers to a machine and software system that integrates with the Polaris integrated library system to sort and track library materials at the IHLS hubs automatically. Depending on the manufacturer/vendor of the system and any purchased add-ons, it may also have additional capabilities.
Updated 2/8/2023
- What Are the Benefits of an Automated Material Handling System?
-
The benefits of an AMH machine may vary, depending on which manufacturer/vendor is chosen and what machine add-ons are purchased.
Potential Benefits to Member Libraries:
- Long-term cost savings for member libraries. AMH systems route items with barcodes instead of labels, saving libraries miles of receipt paper tape.
- Faster delivery turnaround time after weekends and holidays. IHLS sorting staff will be able to sort heavy loads, such as those due to holidays or weekends, in a single day, eliminating backlogs.
- More accurate sorting. Inaccuracy in sorting or delivery was the #2 complaint on the FY2023 IHLS Delivery Survey. The automated material handling system would reduce missorting and the resulting longer delivery times on these items.
- Pandemic-resistant sorting. The low-touch nature of the automated material handling system would make disruption to future pandemics or similar emergencies far less likely.
Bulk check-inandSorting of holds and returns. The AMH can sort items by holds and returns, which is beneficial to libraries with large daily volumes.Additionally, a list of contents of items in an AMH-sorted tub is generated by the AMH system. Libraries can check in all those items at once by scanning a single manifest list barcode, potentially saving library staff time. This can also help prevent chronic injuries due to repetitive movements performed by the circulation staff.Input from the AMH working group has led to an understanding that the benefits of the bulk check-in add-on would not be worth the investment. However, we are still investigating the sorting holds and returns.
Potential Benefits to IHLS:
- Faster delivery turnaround time after weekends and holidays. IHLS sorting staff will be able to sort heavy loads, such as those due to holidays or weekends, in a single day, eliminating backlogs.
- Reduced long-term operating costs to IHLS. Personnel costs would be reduced through decreased total staff hours (likely due to attrition-related staff reductions).
- Increased efficiency through increased speed. The number of items sorted per hour would be much higher, helping staff ensure that all items are sorted every day.
- Reduced likelihood of chronic injury. Sorting bins can be adjusted to the employees’ heights. This provides a safer, ergonomically adjustable workstation for staff, preventing injuries and worker compensation claims.
- Better customer service through more accurate sorting. Inaccuracy in sorting or delivery was the #2 complaint on the FY2023 IHLS Delivery Survey. The automated material handling system would reduce missorting and the resulting longer delivery times on these items.
Updated 3/14/2024
- The AMH Project: What IHLS Is Doing and When
-
- Is IHLS definitely getting an Automated Materials Handling System? For each IHLS location?
-
No. IHLS has been researching the benefits of a system, and we are very interested in what it has to offer. We will only be acquiring an AMH system if we determine that it makes sense to do so.
Updated 2/8/2023
- What is the timeline for the AMH project? Where are we now?
-
The timing of the steps in this project has already changed multiple times and is likely to change again. However, we expect the entire project to take at least two years, if not longer. The stages of this project include:
STAGE 1
1. Form a core AMH staff team. Completed January 2022
2. Informal research. Completed February 2022
3. Decide whether or not to issue a Request for Information. Completed March 2022
4. Writing and issuing a Request for Information (with a third-party consultant). Completed May 2022
5. Analysis of the Request for Information responses (with a third-party consultant). Completed May 2022
STAGE 2
6. Expansion of the AMH staff team and the formation of a member working group. Completed October–November 2022
7. Identify additional research needs and conduct this research (member needs, IHLS needs, machine capabilities, funding options, etc.). Completed January 2023 – March 2023
8. Decide whether or not to issue a Request for Proposal. Working Group recommended to the board to move forward with an RFP. May 2023
STAGE 3
9. Writing and issuing a Request for Proposal (with a third-party consultant). Completed February-March 2024
10. Analysis of the Request for Proposal responses (with a third-party consultant). IN PROGRESS
11. Decide whether or not to proceed with the purchase of one or more machines. Expected May 2024
If IHLS decides to purchase the machines:
STAGE 4
12. Order the machines.
13. Prepare for the installation of the machines / begin the barcode duplication process.
14. Install the machines.
15. Train staff.
16. Begin using the machines.
The above list is not an exhaustive list of all that will need to go into the potential acquisition of an Automated Material Handling System. For example, it does not include the steps IHLS will need to take in working with IHLS member libraries. However, it does provide an idea of the steps required.Updated 3/22/2024
- How It May Affect Member Libraries
-
- Who would be affected by the Automated Material Handling System?
-
The machine integrates with Polaris to sort items, and we believe it can only integrate with a single ILS database at a time. Therefore, the machine would only be capable of sorting items from SHARE-IHLS member libraries. Items from standalone IHLS-member libraries would continue to be sorted by hand.
- What are the benefits to member libraries?
-
The benefits of an AMH machine may vary, depending on which manufacturer/vendor is chosen and what machine add-ons are purchased.
Potential Benefits to Member Libraries:
- Long-term cost savings for member libraries. AMH systems route items with barcodes instead of labels, saving libraries miles of receipt paper and tape.
- Faster delivery turnaround time after weekends and holidays. IHLS sorting staff will be able to sort heavy loads, such as those due to holidays or weekends, in a single day, eliminating backlogs.
- More accurate sorting. While missorting isn't common, it does happen. The automated material handling system would further reduce this occurrence.
- Pandemic-resistant sorting. The low-touch nature of the automated material handling system would make disruption to future pandemics or similar emergencies far less likely.
Bulk check-inandSorting of holds and returns. The AMH can sort items by holds and returns, which is beneficial to libraries with large daily volumes.Additionally, a list of contents of items in an AMH-sorted tub is generated by the AMH system. Libraries can check in all those items at once by scanning a single manifest list barcode, potentially saving library staff time. This can also help prevent chronic injuries due to repetitive movements performed by the circulation staff.Input from the AMH working group has led to an understanding that the benefits of the bulk check-in add-on would not be worth the investment. However, we are still investigating the sorting holds and returns.
Updated 3/14/2024
- Would there be costs to libraries in terms of money, materials, or staff time?
-
Our goal is "no."
The only possible costs that we anticipate for libraries are the materials and labor involved in
re-barcodingduplicating item barcodes.Barcode reduplication on applies if (and only if) libraries:
- are SHARE members
and had barcodes on the inside of their books and audiovisual materials
and don't have RFID.
The following IHLS members would not have to worry about barcode duplication on any portion of their materials:
- IHLS members who are not also SHARE members
- SHARE-member libraries with barcodes on the outsides of their books and audiovisual materials
- SHARE-member libraries with RFID on their books and audiovisual materials
IHLS has been working with staff from both IHLS and several member libraries to come up with solutions for eliminating the costs of
re-barcodingbarcode duplication. Please see "How will IHLS help libraries with barcode duplication?"PLEASE NOTE: IHLS-member libraries do not pay fees to be members of IHLS. Therefore, members would not see any fees related to the purchase or operation of the Automated Material Handling System. We also do not plan for any portion of the costs of the AMH system to be passed along to SHARE-member libraries.
Updated 3/22/2024
- are SHARE members
- How will IHLS help libraries with barcode duplication?
-
In order for materials to be sorted by an Automated Material Handling System, items must be on the outside of the items. It is important to us that we cover the bulk of the burden to our member libraries regarding any required barcoding placement changes, should an AMHS be purchased.
If an AMHS is purchased, IHLS will have these options for helping libraries:
(Learn more about what these options might look like.)OPTION 1: Have IHLS duplicate all eligible barcodes as items pass through an IHLS hub. (In this case, barcodes will be placed on the upper-left-hand corner.)
OPTION 2: Borrow a barcode duplicator from IHLS and have library staff duplicate the barcodes.
OPTION 3: Some of both of the above.Libraries may also choose to do the barcode duplication themselves without the use of an IHLS barcode duplicator.
Updated 3/22/2024
- If my library chooses not to let IHLS do the work for me, how much should I expect barcode duplication to cost?
-
Libraries can use the AMHS estimated costs calculator to find out approximately how much it will cost, should libraries choose to do the duplication on their own rather than allowing IHLS to do the duplication for them.
Barcode Duplication Costs Calculator
Share your results with us!
Are you willing to share your calculator results with IHLS and other libraries? We'd love to hear. (Sharing is completely optional, but it does give libraries and IHLS some additional insight into the costs of an AMH system.)
Submit Your Calculator Results
Updated 3/22/2024
- Barcodes
-
- Does the placement of barcodes on library items matter?
-
Yes. Vendors have informed us that an item's barcode would need to be on the outside of items and not on a spine. For more information, see “Does IHLS or SHARE recommend libraries start putting barcodes in a certain location?”
Updated 2/8/2023
- Will we have to re-barcode our entire collection?
-
No. However, if IHLS installed an AMH system, then some libraries may need to
re-barcodeduplicate barcodes for the portions of their collections that circulate through IHLS delivery. This is because the barcode needs to be on the outside of the item in order to be sorted by the Automated Material Handling System.See "How will IHLS help libraries with barcode duplication?" for more information.
Updated 3/22/2024
- Does IHLS recommend libraries start putting barcodes in a certain place?
-
Yes, IHLS recommends placing printed barcodes on the top-left corner of the front cover of all books and audiovisual items (such as DVDs). This reduces the occurrence of injury to library staff due to repetitive motions. It also makes it easier for circulation staff at all libraries to locate barcodes.
However, this specific placement is not required. For the purposes of the AMHS, barcodes only need to be on the outside of items (any external location except the spine), and this would only apply for IHLS-SHARE members.*
*See "Would there be costs to libraries in terms of money, materials, or staff time?" and "How will IHLS help libraries with barcode duplication?" for more information.
SHARE does not have an official recommendation but supports IHLS Delivery Department recommendations.
Updated 3/22/2024
- What about books with fabric covers, et cetera?
-
There are going to be times when placing a barcode on the outside of an item is not possible or reasonable. That's fine. These items will be hand-sorted rather than sorted through the Automated Material Handling System.
Updated 2/8/2023
- If we have, or switch to, RFID tags (radio frequency identification) on our items, do we also need a regular barcode?
-
It depends.
If IHLS purchases an AMHS, then that system will have RFID-reading capability.
- For SHARE-IHLS member libraries — Yes, your items would need a regular barcode in addition to the RFID tag. Without a regular barcode, SHARE members without RFID scanners would not have a way to scan their items. For the purposes of the AMH machine, the barcodes can still be on the inside when an RFID tag is present. However, IHLS recommends placing all barcodes on the top-left outside corner of the item.
- For standalone IHLS libraries — No, you would not need a regular barcode in addition to an RFID tag.
Please Note: This question was answered incorrectly during the Oct. 20, 2022, IHLS Members Matter meeting and in the meeting recording.
Updated 3/22/2024
- Funding
-
- How much does an Automated Material Handling System cost?
-
We learned from the responses to our Request for Information that the machines vary widely by the vendor in terms of capabilities, base costs, and add-on options. Therefore, we do not have a good estimate of the costs.
In fall 2022, based on the Request for Information responses we received, we learned that costs could range between $250,000 and $500,000 for the unit at the Edwardsville location, with a return on investment for IHLS to be around seven years. (Please note: We previously erroneously reported "$200,000 to $500,00 for the base unit," but the number was actually "$250,000 to $500,000 for the base unit plus add-ons.")
In spring 2023, after seeing and discussing particular machine setups and what IHLS would and would not require in a system, we were able to slightly narrow the range of expected costs to $250,000 to $450,000, with an expected return on investment within six to seven years.
Updated 4/4/2023
- How will IHLS pay for an Automated Material Handling System?
-
We are considering many income streams to pay for the Automated Material Handling System should we move forward with a recommendation to purchase. In addition to money from the general fund, we are considering what grants IHLS could apply for. This will be discussed in further detail with the AMH Working Group should we reach that stage.
Updated 2/8/2023
- Member Feedback and Communication
-
- Is IHLS soliciting member feedback on this project, and how are you communicating with members?
-
Yes, we are soliciting member feedback! This has been on the top of our minds since we started researching Automated Material Handling Systems. We have been and will continue to reach out to members throughout the project, including:
- Seeking IHLS Board feedback (our board is comprised of members and trustees from all four library types).
- Sharing the Request for Information responses and the consultant's review of these responses with the IHLS Board and then making them available to the public through the IHLS website.
- Discussing the Automated Material Handling System project with members during various IHLS Members Matter events, starting with the Oct. 20, 2022, event, and making the recordings available on the IHLS website.
- Surveying members.
- Developing an AMH Working Group comprised of members and staff to help determine member and system needs, research options and opportunity costs, recommend whether or not to issue a Request for Proposal, and provide regular feedback along the way.
- Developing and maintaining a webpage to house AMH project materials, including relevant meeting recordings.
- Develop and maintain a Q&A, housed on the AMH project webpage.
- Provide email updates as needed (this includes updates in the e-newsletter).
Additionally, you may address questions to IHLS Delivery and Facilities Director Colleen Dettenmeier by email or at the IHLS office, 618.656.3216.
Updated 3/22/2024
-
What is the AMH Working Group, and who is on it?
-
The AMH Working Group is an ad hoc feedback and research group comprised of members and staff. This group will help determine member and system needs, research options and opportunity costs, recommend whether or not to issue a Request for Proposal, and provide regular feedback along the way. The AMH Working Group began meeting in January 2023.
The AMH Working Group is comprised of member libraries and IHLS staff. They include eight to ten people from all library types and are primarily, but not exclusively, SHARE members, who will be affected the most. Some of them are representatives from member libraries that already have Automated Material Handling Systems installed at their libraries. The group also consists of staff from IHLS, including our Facilities and Operations Director.
Updated 2/8/2023
- How can one serve on the AMH Working Group?
-
In the fall of 2022, IHLS issued calls for volunteers in our newsletter, on our website, and through social media. We also identified certain individuals who we thought would be particularly helpful, such as individuals from IHLS libraries that already have an Automated Material Handling System. After reviewing the volunteers' library types and sizes, we selected a representative group of individuals to serve on the AMH Working Group.
There are currently no open spots in the AMH Working Group. However, feel free to express your interest to Colleen Dettenmeier by email. She will keep your name on hand in case a spot opens for your library type/size.
Updated 3/22/2024
- Other
-
- Have you thought about the process for those libraries that are not automated (standalone libraries)?
-
IHLS members that are not also SHARE members will have items manually sorted. However, the efficiency improvements of sorting IHLS-SHARE libraries' items would positively affect the IHLS-standalone members' items, too!
Updated 3/22/2024
- Has there been communications with Illinois State Library (ISL) or Reaching Across Illinois Library System (RAILS) on a joint AMH venture?
-
Yes; RAILS looked into an AMH and used the same consultant that we selected. An automated material handling system would not make sense for them, as the many consortia in their area would mean that many separate configurations would be needed. However, Illinois Heartland Library System is different. Our area has one consortium that could be configured to handle the majority (93%!) of IHLS's sorting.
Updated 3/22/2024
- Are any of these automated handling machines equipped with software that could help libraries with IPLAR stats (Illinois Public Library Annual Report)?
-
For SHARE-IHLS libraries, yes. Standalone-IHLS libraries' items would need to be manually sorted and, therefore, would not have any information recorded by the machines.
Updated 2/8/2023
- Why wouldn't IHLS-standalone libraries' items be sorted by the machine?
-
An AMHS works by talking directly with an ILS to identify where an item is headed based on the barcode and routing sequences within the system. Since a large majority of IHLS members use a single ILS, most of the 8.8 million items in SHARE's database could be sorted by an AMHS. In fact, 93% of items sorted by IHLS Delivery come from IHLS-SHARE members. This is why it makes sense for IHLS to couple the power of SHARE with the power of an automated material handling system, even if other items would still need to be sorted manually.
Updated 3/22/2024
- How would this affect staffing at IHLS?
-
In the long term, total staff hours would decrease, and we would likely need fewer people. However, we anticipate that this can primarily be accomplished (and hopefully completely accomplished) through attrition-related staff reductions. Operating an Automated Material Handling System is not staff-free operations; it’s staff-reduced operations.
- Will the “fewer” people need to be there for longer hours? We don’t know for sure.
- Would they be full-time rather than part-time? We don’t know for sure.
- Would drivers sort, now, or at least help stage the items? We don’t know for sure.
Our concern is the staff turnover. We have to frequently hire replacement sorters; over the last 18 months (approx.), of the 11 sorter positions across IHLS hubs, we lost and needed to retrain 1 sorter every 2 months. There’s a definite cost to IHLS for that—about $1,000/sorter for onboarding, administration hours on onboarding and training. This does not include termination costs.
Because of the high turnover, loss of jobs isn’t a major concern. We’ll want to make sure that our staff who do want to stay longer-term are considered. If we decide to purchase and install an automated material handling system, the earliest we anticipate a change would be October 2024; however, it's quite possible that any change would take place later.
Updated 9/14/2023
Project Teams
Many of our staff are involved with the Automated Material Handling System project, from our delivery and facilities director and sorters to our finance and SHARE staff. Additionally, we've formed an AMH Working Group to help us research member needs, analyze costs and benefits, and more. It's important to us that we identify and address our members' concerns.
AMH Internal Team:
As of 3/22/2024 — Leslie Bednar (Executive), Jennifer Baugh (SHARE), Troy Brown (IT), Colleen Dettenmeier (Delivery and Facilities), Aaron Dell (Delivery and Facilities), Laura Flessner (Delivery and Facilities), Shandi Greve Penrod (Communications), Carol Hogan-Downey (Communications), Rhonda Johnisee (Finance), Lia McInerney (Delivery and Facilities), Casey Parr (Delivery and Facilities), Ellen Popit (Membership/Executive), Dena Porter (SHARE), Sarah Taylor (Membership), Angela Thompson (Delivery and Facilities), Cassandra Thompson (SHARE), Brant Wingerter (IT).
AMH Working Group:
As of 3/22/2024 — Staff: Leslie Bednar (Executive), Jennifer Baugh (SHARE), Troy Brown (IT), Colleen Dettenmeier (Delivery and Facilities), Aaron Dell (Delivery and Facilities), Laura Flessner (Delivery and Facilities), Shandi Greve Penrod (Communications), Rhonda Johnisee (Finance), Lia McInerney (Delivery and Facilities), Casey Parr (Delivery and Facilities), Ellen Popit (Membership/Executive) Dena Porter (SHARE), Sarah Taylor (Membership), Angela Thompson (Delivery and Facilities), Cassandra Thompson (SHARE).
Libraries: Mary Cordes (Hayner Public Library District), Esther Curry (CE Brehm Memorial Public Library), Kim Dykstra (Riverton CUSD 14), Lorachelle Eck (Rochester Public Library District), Arlanna Fries (Royalton Public Library District), Kristina Hoerner (Champaign Public Library), Laura Picato (O’Fallon Public Library), Ryan Reitmeier (Taylorville Public Library), Leander Spearman (Belleville Public Library), Sandra West (Rend Lake College). Ex-Officio: Patricia Burg (Illinois State Library).